LED lightning project at Adient Automotive Romania, Timisoara Subsidiary
Contribution to the Virtual Power plant 15,02 kWp
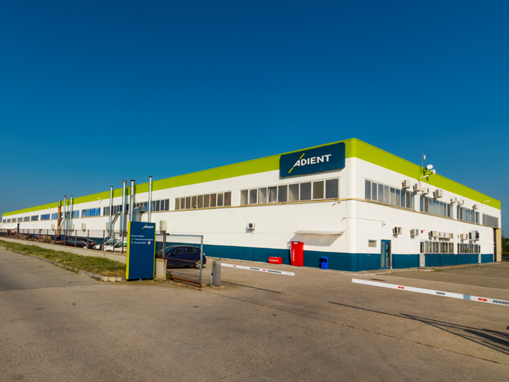
In year 2007, Michel Thierrry Group, one of the textile leading fabricants of the automotive textile industry decided to expand his activity, by opening a new flame lamination plant in Timisoara, Romania. Production started with first RSA/Dacia projects in the month of March 2008, continuing with other projects during the same Year for customers like Volkswagen, PSA, Toyota.
Starting with 2009 the activity has begun to diversify with added value projects involving new processes like pattern embossing, cutting of parts by CNC and die cutting, followed than by serigraphy, embroidery and high frequency welding and also expansion of the client’s portfolio.
In November 2010 Automotive interiors company Johnson Controls has completed the acquisition of the Michel Thierry Group. One important aspect of the company culture refers to development the spirit for sustainable growth witch one of the most important aspects targeted the increasing of the awareness for energetical and environmental aspects at all management and employees levels.
Adient PLC, the automotive seating and interiors manufacturer spun off from Johnson Controls in 2016 following the merger plan with Tyco and Adient Automotive Romania SRL is his Romanian Subsidiary.
The plant in Timisoara is one of the first plants in Romania that invest to change the classical lightning system to led lightning on the entire shop floor and warehouse spaces.
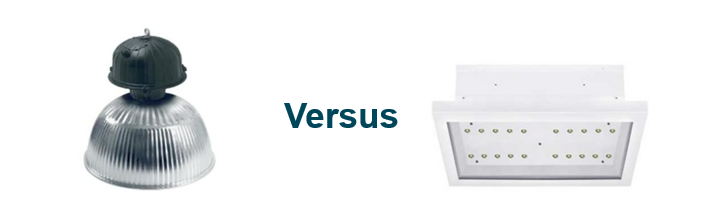
Due the fact it was a brownfield investment, the plant started with classic 400W lamps on entire production and warehouse surface, so that electrical consumption to meet the lightning needs was quite high, mostly in winter period. The comparison of electrical consumption between original lighting elements and new generation of led lightning lamps was revealing a significant energy consumption difference as per below:
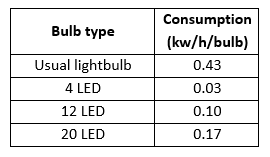
One important aspect to mention in the implementation of this investment was to choose properly the right type of led lightning elements. After making previous light condition determination and definition of the exact desired type of light colour and intensity, we could go to the next step, consisting in identifying providers able to do the works at the required standard and organize the tender. During the tender, these parameters was strictly defined, to ensure that the result will be according to the needs of the plant. Market proved once again that not always the cheapest solution will be also the right one, mostly because, in this case, lightning elements had to fulfil special requirements resulting from work condition constrains.
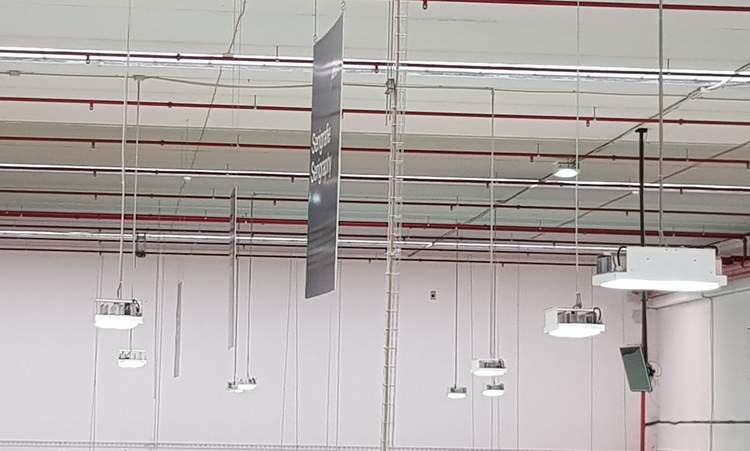
To ensure a proper ROI calculation for the investment approval, after the hourly consumption difference between old and new lamps proposed was defined, the effective utilization hours according work schedule was been taken in account:
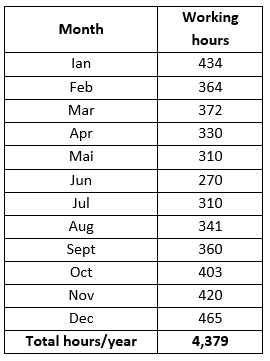
From power consumption point of view, the difference from the old type of lamps to the new type of led lightning elements was decreasing the consumption of electricity from 238.494 KW/Year to 58.214 KW/Year. Making a simple calculation the result obtained show that the consumption using the new system was lowering to a value less than 25% from the initial one.
Financial aspects:
Final investment cost after tender with different suppliers to obtain best condition in price/guarantee/lead time was revealing following costs:
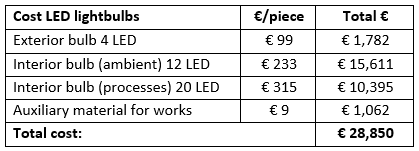
Annual saving taking in account shift pattern for each process was calculated to be 16.117 Euro/year, that leads to a payback time of 1,8 Years.
To be noticed that this calculation is not taking in account the cost for the maintenance of the old lightning elements, that, proportional with their age, can lead to a smaller payback period, due to high cost for lamps and modules replacement on the old lamps.
Even the initial investment shows at the first look a significant value, after taking in account all factors and calculating the return of investment, the financial calculation reveals that this investment is one of the best possible for any kind of plant, no matter of their dimension, to reduce energy and maintenance costs on electricity.
Contribution to the Virtual Power Plant:
- Initial energy consumption: 238.494 kWh/year
- New energy consumption 58.214 kWh/year
- Energy saved: 180.280 kWh/year
PVPPP= QVE x η / τCS
Where:
PVPPP – Energy Saving accounted in the Virtual Power plant
QVE – The full energy saving, meaning the basis of the calculations
η – average powerplant efficiency
τCS – annual peak hours of the power plant
The contribution to the powerplant is: 15,02 kWp