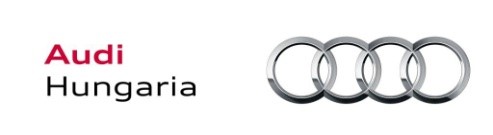
Jelen cikk az Audi Hungaria Motor Kft. gyártási területén üzemelő sűrített levegő ellátó rendszer és a fontosabb technológiai felhasználók felülvizsgálatával, javításával és átalakításával elért energia megtakarításokat mutatja be. A minta gyártósoron elvégzett mérések eredményeit üzemidő arányosan terjesztettük ki az intézkedési körbe vont, de méréssel nem rendelkező sorokra.
This paper shows the energy savings by revision, reparation and modification of the compressed air supply system and large consumer equipments. The results of the measured sample technology were expanded based on running time to similar involved equipments.
A győri üzemi területen kiterjedt sűrített levegő hálózatot tartanak üzemben, és a 6 barg névleges nyomású levegőt elsősorban a gyártósorokon használják fel, pozícionálásra, tisztításra, illetve a szennyeződések távoltartására. A nagyságrendet érzékelteti, hogy a rendszer névleges kapacitása 47 000 Nm3.
A projekt során megvalósított, illetve jelenleg is folyamatosan magvalósítás alatt álló, és ciklikusan ismétlődő intézkedéseket három csoportba lehet sorolni:
- Az ellátó hálózaton végrehajtott ultrahangos szivárgáskeresés, és az erre alapozott javítások
- A nedves megmunkáló gépek ún. zárólevegő fúvatásának optimálása
- Lefúvató kabinok működésének optimálása
A hálózati szivárgásellenőrzés mondhatni logikus intézkedés, nem csak az ilyen kiterjedt hálózatok esetén. A hibahelyek beazonosítását ultrahangos mérőeszközzel végezte szakvállalkozó, majd ezek javítása már a gyártósori karbantartók feladata volt. A tipikus hibák a csatlakozó szerelvényeknél, szűrőpoharaknál és az végpontoknál adódtak. Minden egyes javítás sikerességét méréssel ellenőrizték, és megállapították a javítás sikerességét, mivel nincs minden esetben tökéletes megoldás, valamint értékelni kellett a ráfordítás és a várható eredmény arányát is. 2015-ben 1547 db szivárgási helyet azonosítottak és javítottak meg a hálózaton, amire egy példát mutat az 1. ábra.
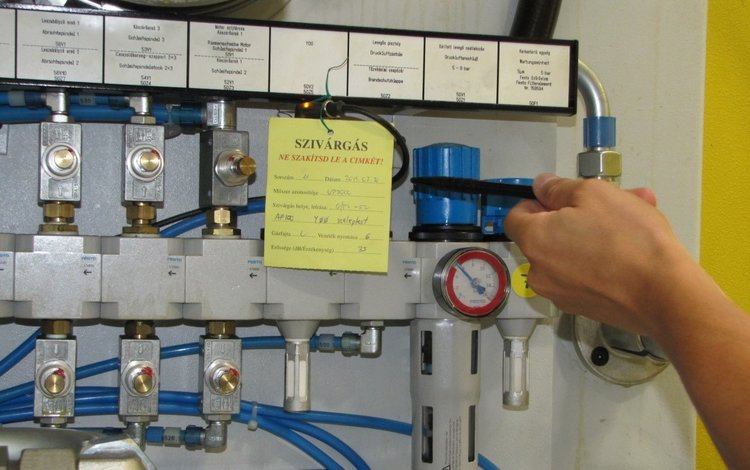
A mérési eredmények alapján az elszökő levegő mennyiségét is meghatározták, aminek villamosenergia igényét a sűrített levegő termelés fajlagos felhasználásból lehetett kiszámolni. A hibajavítások költségeivel a megtérülési idő könnyen számítható volt, és átlagosan 0,43 hónapra adódott.
A rendszeren természetesen lényegesen több szivárgási hely ismert, illetve sejtett, de a tapasztalatok az mutatják, hogy a javítások utáni évben a szivárgási helyek legfeljebb 60%-át azonosítják újra, de veszteségre vetítve ez 50% alatti értéket jelent. Szintén tapasztalat, hogy a feltárt veszteségek átlagosan 85%-át tudják a megszűntetni különböző korlátozó tényezők miatt. Egy éves felülvizsgálati ciklusidő esetén a vizsgálat költségéből adódóan a megtérülések éven felüli értékre adódtak, így az egyes szakaszokon a hibakeresés ciklusát két évre állították be az üzemeltetők. A 2015-ös évben a korábban program indítása óta megvalósított javításokat is elszámolva a megtakarítás mértéke 3 753 Nm3/h, ami 3,63 GWh/év villamosenergia felhasználás, és 1 454 t/év CO2 kibocsátás csökkenésnek feleltethető meg.
A másik két intézkedés a gyártáshoz köthető, és sikerességüket – az Audi Hungária Motor Kft. gyártási területén még 2013-ban kialakítani kezdett – a termelő berendezések energiafelhasználását monitorozó minta gyártási sor létrehozása alapozta meg. Ennek keretében egy kiválasztott gyártósor elemeit látták el az energiafelhasználás mérésére alkalmas eszközökkel fokozatosan. A mérések alapján számos intézkedést foganatosítottak az ott dolgozók, majd 2014-re fókuszba került a sűrített levegő felhasználás csökkentését célzó megoldások keresése is.
A mért értékek elemzése meglepő eredményeket hozott, elsősorban a technológusok számára. Kiderült, hogy a vizsgált, 41 db technológiai elemből álló gyártósor heti sűrített levegő fogyasztásának nagyjából 56%-áért mindösszesen 7 berendezés volt felelős, amiből 6 nedves technológiájú köszörűgép.
A forgácsoló berendezések esetén az emulzió nem kívánt helyekre történő bejutását ún. záró levegő fúvatásával érik el. A vizsgálatok azt mutatták, hogy technológiai szokások és az üzemeltetési rend alapján komoly potenciál mutatkozik ezen a területen. Kiderült, hogy a heti felhasználás 7,8%-át a vasárnapi üzemszüneti napon is felhasználták a berendezések, ráadásul úgy, hogy az azonosított 7 nagyfogyasztó mellett mindössze egy berendezésen volt értékelhető fogyasztás. Az elemzés során fény derült rá, hogy a gépeken felhasznált levegő mennyiségét alapvetően befolyásoló helyi nyomásszabályozást a kezelők megszokás alapján állították 0,3-0,9 barg között, valamint a zárólevegő állásidő alatt is folyamatosan felhasználásra került. Ebből eredően a fogyasztáscsökkenést a helyi nyomáskülönbség gép specifikus beszabályozása, továbbá az üzemidő PLC programozással elérhető csökkentése jelentette.
A folyamatos mérésnek köszönhetően az elért eredmények pontosan rendelkezésre álltak, így megállapítható volt, hogy a heti fogyasztáscsökkenés közel 13 000 Nm3/h volt, ami 14,3%-ot jelentett. Vasárnaponként a csökkenés ~5 800 Nm3/h-át ért el, ami 82,3%-nak felelt meg.
A projekt több, mint 1000 db megmunkáló gépet érint a gyár területén, és az indulás óta nagyjából 400 gépet sikerült beállítani. A 2016-os terv 250 db, elsősorban a régebbi berendezésekre koncentrálva. A 2015-ös elszámolás készítésekor az eredményeket 25 db, a tesztelt gyártósorhoz hasonló, vagy azonos felépítésű, ám méretlen sorra terjesztették ki.
A harmadik projektelem a lefúvató kabinok működésének optimálása volt. Ezekben a kabinokban a megmunkált munkadarabok sűrített levegővel történő tisztítása történik, ami elsősorban a forgács eltávolítását és a hűtő-kenő folyadéktól való mentesítést jelenti. A munkafázis felülvizsgálatakor az alábbi problémákat tárták fel a technológus kollégák:
– helytelen időzítés: a munkadarab még sokszor a helyén sem volt, amikor a lefúvatás már megkezdődött
– egyidejű teljes lefúvatás: a fúvóka csoportok ún. palettákon kerültek kialakításra, és ezek mindegyikén egyszerre, folyamatosan történt a lefúvatás, ami gépenként akár 1 000 Nm3/h-ás fogyasztási lökéseket jelentett a hálózat irányába
– fúvókák rossz beállítása: munkadarabtól függően számos olyan fúvókát találtak a felülvizsgálók, amelyeken feleslegesen, vagy rossz irányban áramlott a levegő
– feleslegesen nagy nyomás: üzemi vizsgálatok kimutatták, hogy a 6 barg-os hálózati nyomás helyett elegendő lenne a kívánt eredmény eléréséhez 3 barg-os levegő is
– feleslegesen nagy ütemidő
A problémák felismerésekor, a gyártervezési és gyártástervezési osztályok kollégái egy régebbi berendezés átalakításával tesztberendezést hoztak létre, ahol az átalakítások hatásait elemezni tudták, miközben a gyártás folyamatos maradhatott. Itt lehetett tesztelni a fúvókák különböző iránybeállításait, a palettákon való elhelyezésüknek változatait, a nyomáscsökkentés korlátait és az elegendő ütemidőt. A legizgalmasabb kísérletek a paletták üzemidő eltolásának, illetve az impulzus jellegű ún. lesöprő lefújások számítottak. Ezzel el lehetett érni, hogy a fogyasztási lökések gyakorlatilag eltűntek, ami csökkentette a – más berendezésekre nézve kritikus – hálózati nyomásingadozás kockázatát. Egy motorblokk lefúvató berendezésen megvalósított beállításokhoz tartozó mérési eredményeket mutat be a 2. ábra. Látható, hogy a fúvókacsoportok lefúvási idejének eltolásával, és a fúvókák beállításával a csúcsfogyasztás mintegy 60%-ra esett vissza, majd a nyomás csökkentésével, és az üzemidő kísérleti beállításával, a felhasznált levegő mennyiség 66%-kal volt csökkenthető.
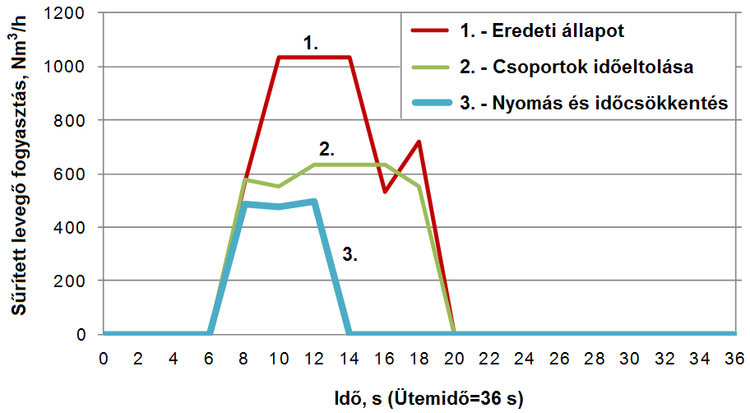
A visszamért berendezések átlagos megtakarítási értékeit 90 átalakított berendezésre terjesztettük ki, figyelembe véve a gyártott darabszámokat is.
A három intézkedés típus által elért megtakarításokat a 2015-ös évben mintaprojektek eredményeire támaszkodva, illetve a közvetlenül mért eredményekből lehetett meghatározni. Ezek értelmében villamos kapacitás csökkenéssel nem számoltunk, mert a csúcsok levágásával csak az üzemvitel biztonsága javult. A fogyasztás maximális órai csökkenése 17 887 Nm3/h-t jelentett, ami a darabszámok és az üzemidők figyelembevételével 6,65 GWh/év villamosenergia megatakarításnak felel meg 2 226 t/év CO2 kibocsátás csökkenés mellett (1. táblázat).
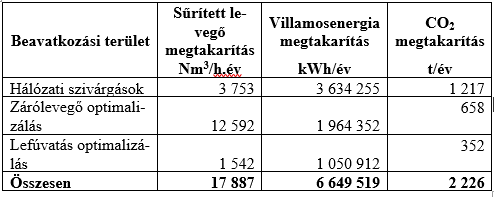
A Virtuális Erőmű elszámolási rendszerében a megtakarított villamosenergia mennyisége közvetlenül elszámolható, és értéke:
ΔEv = 919,4 kW
A projektek további hozadéka, hogy a technológus és energetikus kollégák felismerték, hogy a fogyasztók jelentős részét át lehetne alakítani 3 barg nyomásszintű üzemre. Ennek természetesen akadálya, hogy az üzemben ez nem áll rendelkezésre, illetve a gyártói oldalon a 6 barg olyan bevésődött érték, amit csak a megrendelések pontos specifikációjával kényszerítve lehet megváltoztatni. A párhuzamos hálózat kialakítása jelentős költség, de a nyomáscsökkentés újabb számottevő megtakarítás forrása lehet.
Köszönetnyilvánítás:
A cikk elkészítéséhez pótolhatatlan segítséget nyújtott az Audi munkatársai által elvégzett munka, akik közül a teljesség igénye nélkül került kiemelésre: Kiss Péter, Dr. Ozsváth Péter, Spirk László és Tóth Tamás.